The central aim of automated building management systems (BMS) is to maintain a facility’s correct operation while maximising its efficiency. The BMS controls major subsystems like HVAC, hot water and central heating, chilled water, etc. It is designed to monitor these subsystems for critical failures and generate alerts accordingly—but without the right analytics, these alerts can quickly turn into data overload and “BMS alarm fatigue.”
BMS receive data from a wide array of sensors, from lighting systems to HVAC. They often display dozens of interrelated alerts without indicating how they are connected, which tasks are high priority, or what actions should be taken to resolve them.
In our recent report on energy blind spots, we found that facility managers receive an average of 12.5 alarms per day, with more than 50% receiving up to 30 alarms daily. With such high volume, it’s no surprise that urgent alerts are getting drowned out by background noise.
BMS alarm fatigue can cause delayed or missed responses to genuine alarms, with profound ramifications for energy consumption, thermal comfort, and building safety.
Fortunately, data analytics can help prioritise alarms, making it easy to identify and action the ones that matter most. In this article, we’ll explore how leveraging the right data can prevent BMS alarm fatigue and keep your buildings operating as efficiently as possible.
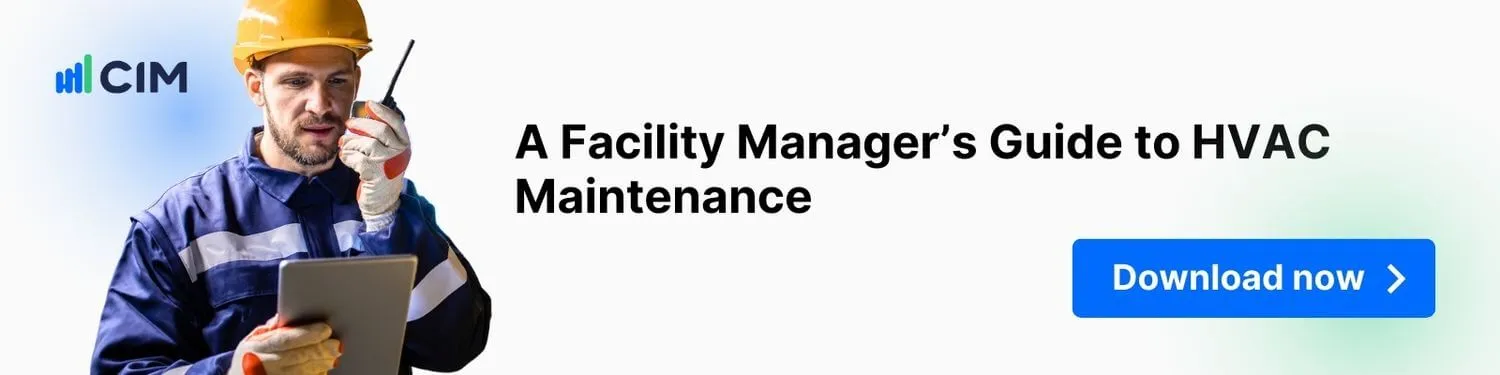
Jump Too:
What causes BMS alarm fatigue?
The true cost of HVAC inefficiencies?
A preventative strategy is the key to controlling maintenance costs
The impact of analytics data on HVAC efficiency
Identify and prioritise the actions with the biggest impact
The PEAK platform cuts through the clutter
How does CIM ensure we don't add to alarm fatigue?
What causes BMS alarm fatigue?
Our survey found that one in three facilities managers feel their BMS wasn’t adequately commissioned. This process is usually done under time pressure—not to mention by the BMS vendor themselves—so quality can suffer. Additionally, only 24% of facility managers say their BMS is actively helpful in identifying HVAC issues that create inefficiency. A whopping 76% feel there’s room for improvement.
Further, identifying operational improvements is outside the scope of work for most BMS vendors. Their job is to maintain conditions; improving your site’s energy efficiency is likely not a part of their brief.
With more than half of facility managers reporting as many as 30 alarms per day, it’s no wonder most feel their BMS is a less-than-perfect diagnostic tool.
BMS alarm fatigue can result from a host of contributing factors:
- Repetitive alarms
- Redundant alerts
- Incorrect settings
- Faulty hardware
- Unactionable alerts
When your inbox is flooded with dozens of daily alarms, the urgent and actionable can easily get lost in the fray. While two-thirds of our survey respondents receive BMS alarms, only one-third react to them.
And for each day that passes without action on high-priority issues, the cost impact can be significant.
The true cost of HVAC inefficiencies
HVAC-related alarms are particularly important, because HVAC systems are the biggest single contributor to a building’s energy costs. Yet many facility managers are left scrambling in reactive mode to address critical errors—not to mention inefficiencies.
One in every three facilities isn’t currently leveraging data to identify high-value HVAC priorities. Nearly two-thirds say they are deficient in data collection and analysis for HVAC, and 40% have a reactive HVAC maintenance strategy.
In other words, facility managers often don’t have the tools to get out ahead of the challenges they face on a daily basis. They respond to crises as they happen, rather than benchmarking performance via historical data and sharing lessons learned with their sister sites or even their peers.
In part, that’s because poor BMS commissioning and legacy systems are hampering rather than helping BMS control. As Conor Murray of ASHRAE Ireland has said, “Without accurate, reliable, and relevant data, you cannot make intelligent decisions around HVAC.”
There’s often a gap between the lofty promises of data analytics and the gains that building owners and facility managers realise. This gap in identified versus actual savings comes down to the inability to triage issues in real time and separate critical alarms from white noise.
A preventative strategy is the key to controlling maintenance costs
A BMS alarm is only as good as its resulting action, but most sites can’t quickly identify next steps or triage based on priority. The BMS knows if an alarm is critical, but it can’t recognise opportunities to optimise equipment in advance or deliver operational improvements.
Building analytics software helps create a preventative strategy based on data, enabling a condition-based maintenance routine rather than one that centres on frequency.
To illustrate this point, we’ll use John as an example. John is a facility manager who works with multiple legacy systems, each on a separate PC: BMS, CHP, thermal oxidisers, wastewater treatment plants, etc. …. All of these run on a plethora of separate platforms with no interconnectivity.
John is frustrated by the lack of transparency inherent in this setup, which leaves him at the mercy of third-party contractors. His role is highly reactive; he’s constantly juggling priorities and has no time to think strategically about how to reduce spend and hit carbon emission targets. Moreover, John is working toward these goals in the midst of a perfect storm. Ever-increasing energy prices and carbon dioxide reduction targets actively thwart his efforts. He faces a multitude of new challenges without the resources to overcome them.
Fortunately for John, building analytics provide an opportunity for prompt, clear ROI on a number of levels. By surfacing the best opportunities for efficiency gains, particularly within HVAC systems, analytics save John hours of time, effort, and data overwhelm.
Using CIM’s PEAK Platform, John can quickly and easily identify the BMS alarms that genuinely require action. He knows which specific actions to take next and which alarms he can safely deprioritise. Armed with targeted data, John is well-equipped to achieve his operational and budgetary targets.
The impact of analytics data on HVAC efficiency
High-value tasks like HVAC system improvements or repairs can be identified quickly with building analytics, preventing unplanned downtime and avoiding costly mishaps.
HVAC analytics software can reduce energy costs by:
- Assisting with maintenance: Ensuring adequate maintenance regimes (condition-based instead of schedule-based)
- Tracking excessive operation: Reduce equipment runtime when it’s no longer needed
- Ensuring suitable installation: Remove control point overrides, ensure proper physical installation, and verify that control algorithms are operating correctly
BMS alarms are only as effective as we make them. Building analytics tools like CIM’s PEAK Platform transform alarms from a pain point into what they were always intended to be: a powerful tool that helps facility managers and building owners meet their objectives.
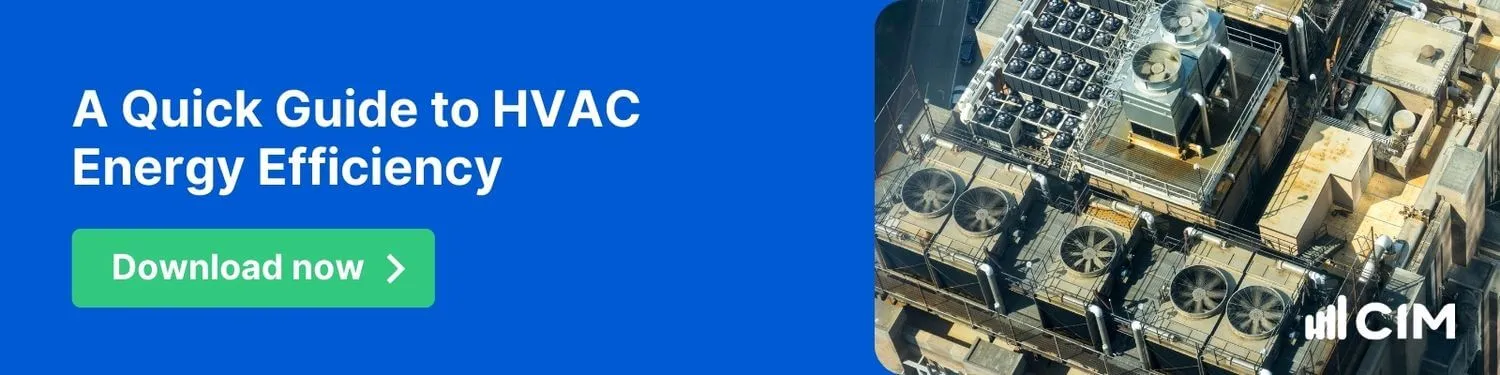
Identify and prioritise the actions with the biggest impact
As BMS alarm fatigue demonstrates, the solution to a building’s HVAC and other systems inefficiencies isn’t more data. The solution is leveraging the right data to help bypass the white noise and take the actions that matter most for your budgetary and environmental goals.
When facility teams know precisely where and how to take action, efficient and cost-effective operations will follow.
The PEAK Platform cuts through the clutter
Enter CIM’s PEAK Platform, engineered to fight alarm fatigue by offering relevant, actionable alerts. Our approach towards rules and alerts is different; we concentrate on relevance and prioritisation. Our data attests to this approach, with less than 7.8% of all alerts muted by users. That means over 92% of our alerts are considered highly relevant and actionable.
Our commitment to maintaining the relevance of our alerts and the quality of our rules library is clear and a testament to our adaptability, action-oriented mindset and continuous learning. As an example, only 1% of PEAK’s rules have triggered an alert at a particular site. In contrast, despite containing less than half the number of rules, 73% of a competitor’s rules triggered alerts - an overwhelming and unsustainable figure.
Simply put, we have more high-quality rules, but fewer alerts, thus reducing the 'noise' and helping operations teams action the real issues. Activity is also prioritised, as users can quickly and easily assign their Actions inbox by priority ensuring issues are being addressed based on impact. This focus on highlighting the real issues is central to our strategy to combat alarm fatigue and remain as a trusted partner to operations teams globally.
How does CIM ensure we don't add to alarm fatigue?
So how do we keep our growing library of algorithm-based rules so relevant? Just like our platform constantly monitors complex networks of plant and equipment, we are always keeping abreast of platform usage patterns and customer feedback. We learn from our users about their shifting pain points and priorities to inform both front- and back-end product evolution.
From the perspective of rule creation, the ‘3C’s Principle' ensures we are only creating rules that will resonate and drive impact.
- Care: We ensure that users care about the outcome of the rule by targeting issues impacting thermal comfort, maintenance, energy, and other focus areas.
- Clarity: We ensure our rules are clear in description and provide straightforward next steps, even for a non-technical audience.
- Confidence: We ensure our rules don't overlap and that the issues they identify are accurate and reliable.
When the only alerts created are those that truly matter, the associated actions are closed at higher rates. This ensures value is constantly being unlocked in terms of energy reduction, increased equipment lifecycle and sustainability rating upside. For example, more than 3,000 PEAK actions were closed at a closure rate of 82% across Charter Hall’s portfolio of office properties.
In our client’s words
Our users attest to the efficiency of our approach. Instead of adding to noise and BMS alarm fatigue, our clients agree that significant operational value can be unlocked by supplementing their BMS with PEAK. By working together harmoniously, the two can drive lasting operational efficiencies.
Our platform not only alerts them of issues in their HVAC systems but also of issues that the BMS might have missed.
“We have learned about issues related to our facilities which we never knew we had! As a manager of the facility, I have far more visibility and awareness than I would have with the BMS alone.” - Engineering and Facilities Manager, UK
“It’s great being able to pull trends from different buildings all in the one platform. Gone are the days of having to log into an individual BMS for each building which is not only time consuming, but with cyber security constraints within large organizations, getting access into the BMS is becoming increasingly difficult.” - WA Technical Lead, Australia
“It’s picked up on issues with the BMS and HVAC equipment that we otherwise wouldn’t have known about. Working with CIM has been great as they have helped us to navigate the site and also to change the parameters as required.” - Building Manager, Australia
It’s this positive user feedback that helps us stand out, with a 4.6 out of 5 star average on Capterra and a 35 NPS.
Concluding
In a world awash with data, the challenge is filtering out the noise to find the real value. The PEAK Platform does just that, fighting against alarm fatigue and helping Facility and Operations Managers focus on what truly matters. With a commitment to making alerts more relevant, listening to users' feedback, and a constant learning mindset, we're confident of providing our clients with a platform that is not just another source of noise, but a tool that truly aids in their operations. We look forward to continuing to help our clients rise above the noise and operate their properties more effectively.
See how CIM’s PEAK platform can power a data-driven approach to maintenance that has proven to be a smarter, more efficient, and more cost-effective solution than the traditional reactive approach. Watch a demo session of our innovation PEAK Platform here.