Modern commercial buildings demand more than just functioning HVAC systems—they require optimized, efficient, and fully integrated solutions. That’s where HVAC commissioning comes in. Whether you’re developing new infrastructure or retrofitting existing systems, commissioning ensures your HVAC investment performs to its full potential.
In this guide, we’ll explain what HVAC commissioning is, why it matters, and how to execute it effectively—with a focus on checklists, software, and reporting.
What is HVAC commissioning?
HVAC commissioning is the quality assurance process of verifying that a building's heating, ventilation, and air conditioning systems are designed, installed, tested, and capable of being operated and maintained according to the owner's operational requirements.
It involves comprehensive inspection, testing, and documentation to ensure every HVAC component functions as intended—from air handlers and chillers to control systems and ductwork.
The purpose of HVAC commissioning
The primary goals of HVAC commissioning are:
- Optimal Performance: Ensure systems operate as designed for comfort, energy efficiency, and air quality.
- Reduced Operational Costs: Identify and correct inefficiencies that can lead to inflated utility bills.
- Regulatory Compliance: Meet building codes, green building certifications, and other regulatory standards.
- Minimized Risk: Prevent costly failures, warranty issues, and user complaints.
The HVAC commissioning process: step-by-step
HVAC commissioning is a structured, multi-phase process that ensures all systems perform to the design intent and operational requirements. Each phase builds on the previous, combining rigorous planning, collaborative execution, and ongoing optimization. Below is a breakdown of the commissioning process from concept to post-occupancy.
1. Pre-design phase: defining the vision
This foundational phase lays out the expectations for system performance and helps align all stakeholders.
- Owner’s Project Requirements (OPR): The commissioning authority (CxA) works with the owner to define performance goals, environmental objectives, energy targets, and occupant comfort needs.
- Commissioning Plan: A draft plan is created to outline the scope, schedule, team responsibilities, and communication protocols.
- Team Engagement: Early involvement of architects, MEP engineers, and the CxA helps embed commissioning in the project lifecycle.
Why it matters: Establishing clear goals early prevents scope creep and ensures all design decisions align with operational priorities.
2. Design phase: translating intent into strategy
This phase ensures that design documents are aligned with the OPR.
- Basis of Design (BoD): Engineers document the technical approach to meeting the OPR, including equipment selection and control strategies.
- Design Reviews: The CxA reviews drawings and specifications to catch issues early (e.g., oversized equipment, conflicting control sequences).
- Commissioning Specifications: These are embedded in the project documents to require contractor participation in the commissioning process.
Pro tip: Catching discrepancies between OPR and BoD here reduces costly changes during construction.
3. Construction phase: verifying installation integrity
This is where plans become physical systems, and quality assurance takes center stage.
- Submittal Review: The CxA verifies that selected equipment matches specifications.
- Installation Observations: Field inspections ensure equipment is installed correctly, accessible for maintenance, and safe to operate.
- Pre-functional Checklists: Contractors fill out detailed forms verifying that components (e.g., dampers, pumps, VAVs) are ready for testing.
Common errors caught: Incorrect wiring, sensor placement, inaccessible equipment, uninsulated piping.
4. Functional performance testing: proving the system works
This is the heart of the commissioning process—where systems are tested under real operating conditions.
- Test Protocols: The CxA develops test procedures for each system and sequence of operation.
- System Testing: HVAC equipment is tested individually and as an integrated system (e.g., AHUs, chillers, boilers, VAV boxes, controls).
- Deficiency Resolution: Any issues are logged in a commissioning issues log and resolved collaboratively with the contractor.
Tests include: temperature control, airflow verification, occupancy sensor logic, emergency shutdown response, and trending data.
5. Turnover and occupancy phase: equipping the operators
Now that the systems are performing, it’s time to empower the building staff to operate and maintain them.
- Training Sessions: Facility personnel are trained on controls, maintenance procedures, alarm systems, and troubleshooting.
- Systems Manual: A comprehensive guide including O&M manuals, as-built drawings, and commissioning documentation is delivered.
- Seasonal Testing (if required): Certain systems (like boilers or economizers) may require off-season testing to verify year-round functionality.
Well-trained operators are key to preserving the benefits of commissioning over the long term.
6. Post-occupancy and ongoing commissioning
Commissioning doesn’t stop at occupancy—ongoing validation ensures systems continue to perform.
- Trend Review: Energy use and HVAC system data are monitored over time (especially with analytics software like the PEAK Platform).
- Re-Commissioning or Monitoring-Based Commissioning (MBCx): If performance drops, systems can be re-optimized using real-time data.
- Lessons Learned: Feedback from operations and occupants informs future design and operational improvements.
Buildings that undergo ongoing commissioning have been shown to reduce energy use by up to 15% compared to those that don’t.
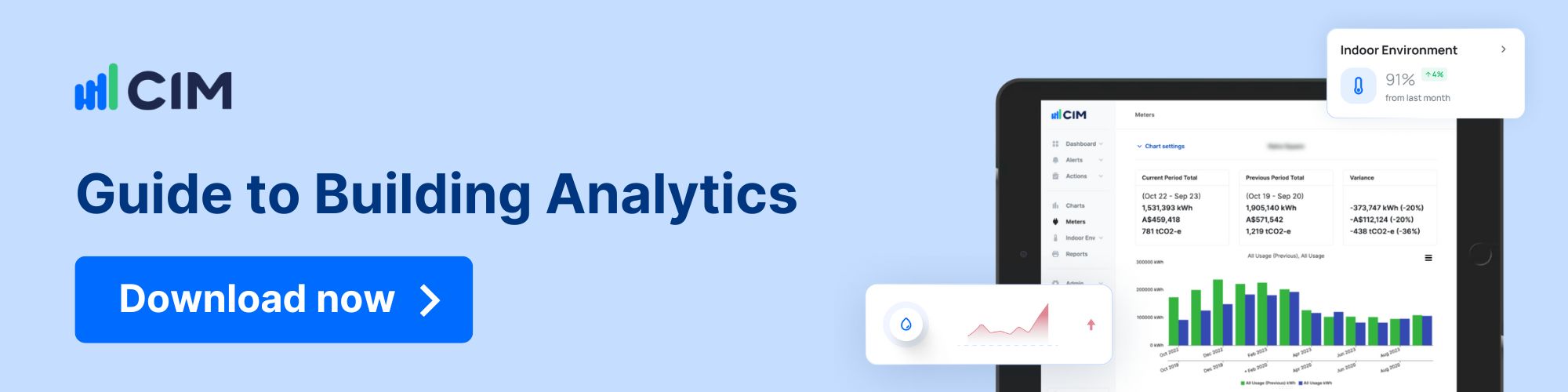
HVAC commissioning checklist:
A commissioning process is only as effective as the checklist that guides it. The HVAC commissioning checklist is an essential tool that helps ensure nothing slips through the cracks—covering all critical components from design validation to final handover. It acts as a roadmap for contractors, engineers, and commissioning authorities (CxAs) to verify that HVAC systems are safe, efficient, and fully functional.
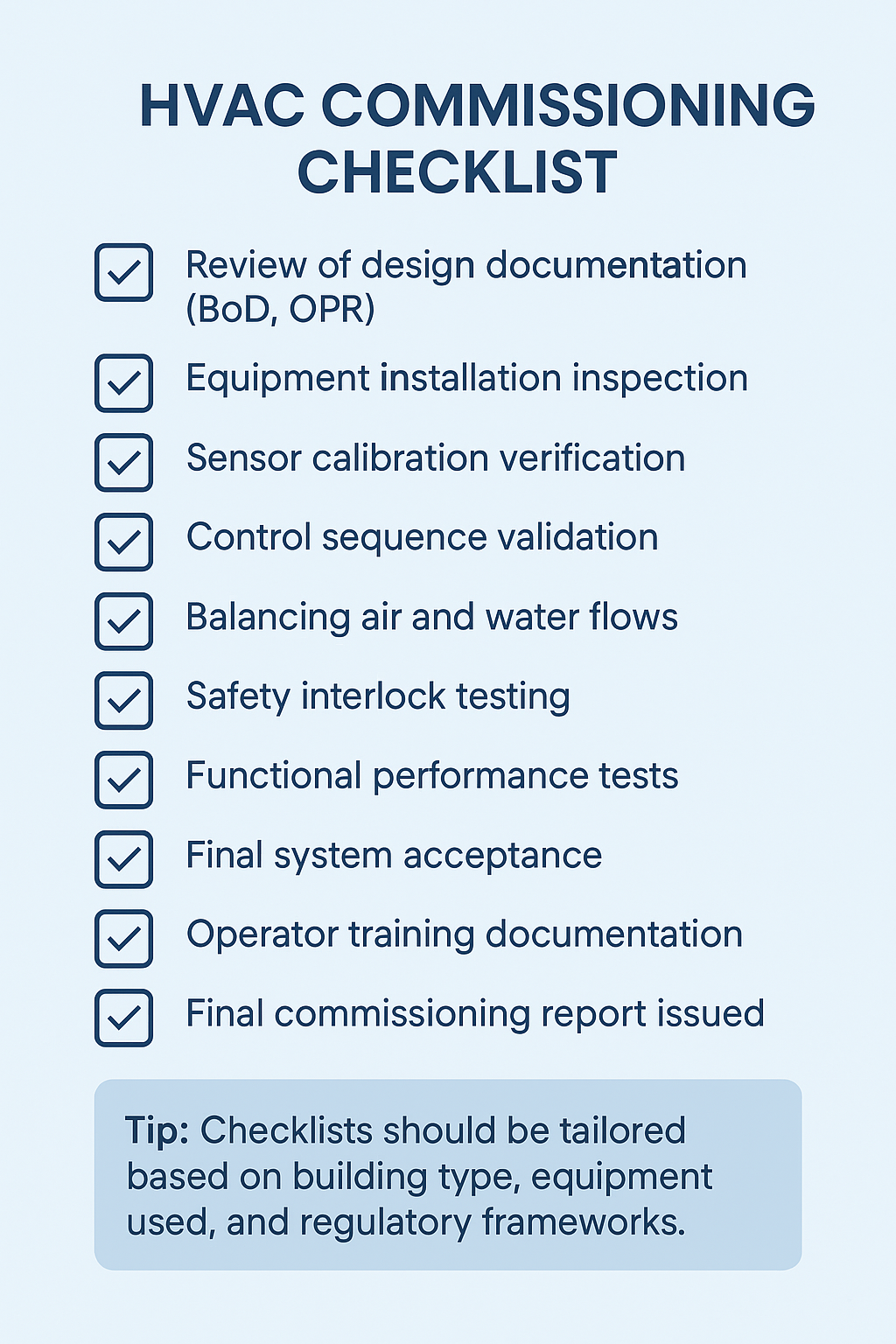
What does the checklist include?
Here's a breakdown of what a well-rounded HVAC commissioning checklist typically covers:
1. Review of Design Documentation
Before a single component is installed, verify that the Basis of Design (BoD) and Owner’s Project Requirements (OPR) are aligned. This ensures the system is engineered to meet performance expectations, energy goals, and occupancy needs.
- Ensure equipment sizing matches the load calculations
- Confirm zoning layouts, duct routing, and control strategies
- Identify and resolve conflicts early
2. Equipment Installation Inspection
Proper installation is foundational. A mismatch between the design intent and on-site execution can lead to costly inefficiencies.
- Check that AHUs, chillers, boilers, and pumps are installed as specified
- Verify access for maintenance and service
- Confirm correct orientation, insulation, and labeling
3. Sensor Calibration Verification
Sensors are the nervous system of any HVAC system. If they’re inaccurate, the entire control strategy suffers.
- Validate temperature, humidity, and pressure sensors
- Ensure calibration matches manufacturer specs
- Confirm sensor placement avoids heat sources or air drafts
4. Control Sequence Validation
Modern HVAC systems rely heavily on automation. This step ensures the Building Management System (BMS) or other controls execute sequences of operation correctly.
- Test economizer logic, VAV modulation, and demand-based ventilation
- Simulate occupied/unoccupied modes and emergency shutdowns
- Verify alarms and alerts are functional
5. Balancing Air and Water Flows
Improper balancing leads to hot/cold spots, noisy ducts, and energy waste.
- Air balancing of terminal units (VAVs, diffusers)
- Water balancing of chilled/hot water loops
- Ensure design flow rates are achieved and documented
6. Safety Interlock Testing
Safety comes first. These checks confirm the system responds correctly in abnormal conditions.
- Smoke detector shutoffs
- Pressure relief valve functionality
- Emergency power-off switches
7. Functional Performance Tests (FPT)
FPT is where the rubber meets the road—proving that every system functions as intended under load and in realistic conditions.
- Run AHUs through start/stop cycles
- Measure response times to control changes
- Log BMS trends and performance data
8. Final System Acceptance
After resolving all issues and deficiencies, the system is evaluated one last time to confirm it meets project requirements.
- Walkthroughs with the commissioning authority and owner
- Punch list resolution
- Sign-off from all stakeholders
9. Operator Training Documentation
A well-trained team is crucial for sustaining performance gains.
- Conduct hands-on training sessions for facility staff
- Provide manuals, maintenance schedules, and quick-reference guides
- Document all training activities
10. Final Commissioning Report Issued
This comprehensive document captures all testing, verifications, and issues resolved.
- Includes executive summary, system overview, test data, and recommendations
- Becomes a legal and technical reference for the life of the building
- Supports warranty claims and future re-commissioning efforts
Pro tip: Tailor the checklist to your specific project. Factors such as building type, HVAC system complexity, equipment manufacturer requirements, and regional regulations should all influence the checklist design. Tools like commissioning software or digital templates can simplify this customization.
Types of HVAC commissioning software
HVAC commissioning software plays a pivotal role in ensuring that heating, ventilation, and air conditioning systems are designed, installed, tested, and maintained to meet the owner's operational requirements. These software solutions enhance accuracy, standardization, and documentation throughout the commissioning process. Below are the main categories of HVAC commissioning software, along with examples and their key features:
1. Field data collection platforms
- Example: CxAlloy, BlueRithm
- These tools are designed for on-site use, enabling technicians to collect data, complete checklists, and document issues in real-time.
2. Analytics & fault detection platforms
- Example: PEAK Platform by CIM, SkySpark
- These platforms focus on post-commissioning activities, providing continuous monitoring and performance validation to ensure systems operate efficiently over time.
3. Documentation & workflow tools
- Example: Facility Grid, Flowdit
- These tools streamline the management of commissioning documentation, task assignments, and compliance tracking.
By leveraging these HVAC commissioning software solutions, professionals can enhance the efficiency, accuracy, and reliability of the commissioning process, leading to better-performing HVAC systems and increased client satisfaction.
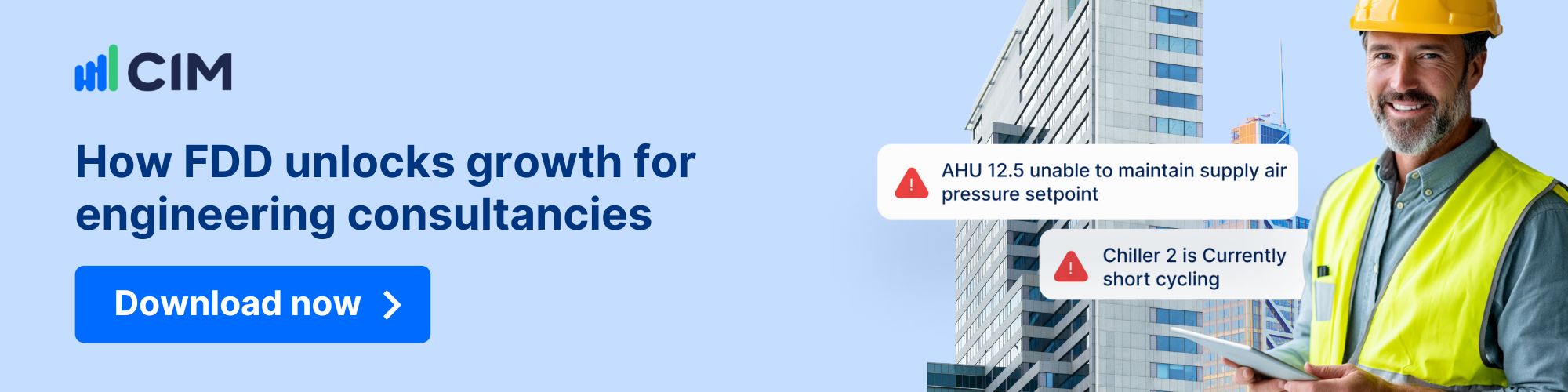
Commissioning report for HVAC
The commissioning report is the culmination of all testing, inspection, and verification activities. It serves as a legal and technical record.
Key Components Include:
- Executive Summary (scope, systems covered, key findings)
- Pre-functional and functional test results
- Issues log and resolution tracking
- Performance metrics (e.g., temperature stability, energy use)
- Recommendations for improvement
- Warranty information and equipment manuals
- Operator training records
A good commissioning report is both a compliance document and a practical guide for facility teams.
Conclusion
HVAC commissioning is a smart investment that ensures your systems operate efficiently, meet performance goals, and deliver long-term value. With a structured process, modern tools, and clear documentation, you can maximize comfort, compliance, and cost savings across your building’s lifecycle.
Interested in taking HVAC performance a step further?
Learn how continuous monitoring through analytics platforms like CIM’s PEAK Platform extends the value of commissioning and identifies hidden inefficiencies over time.
👉 Book a demo of the PEAK Platform to see how real-time insights can optimize your building operations.